前回の製作記事で登場したラディアスディッシュの詳細と作り方を説明します。
前回記事↓
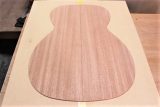
ラディアスディッシュ↓
こちらはバック用の物になります。ラウンド具合は15feet(半径約4m50cm)で作っています。15feetの大きな円周の一部がラウンド形状となります。
ラディアスディッシュはアコギのトップ板とバック板のラウンド形状を作るのに必要な冶具です。
絶対に必要というわけではありませんが「均一で綺麗な仕上がりのラウンド形状」にしたい場合は必要です。ちなみにラウンド形状にする工程を「ドーミング」と呼んだりします。
バック板がラウンド形状になっている仕様の事を「ラウンドバック」と呼んだりしますがこのワード自体は耳にしたりする人も多いのではないでしょうか。
「そもそもラウンド形状ってなに?」という方もいるかもしれません。
簡単に説明するとアコギのバック板はよく見ると中央部分にかけて膨らんでいます。この膨らみがあるバックはラウンドバックという事になります。逆にあまり見かけませんが膨らみがほとんどない物に関してはフラットバックと言います。僕が学生時代に作った事があるのは製作が容易という事でフラットバックでした。
ではトップ板はどうでしょう?
トップ板に関しては「フラットトップ」と呼ばれる仕様が定番です。
ただしこれには多少の矛盾があり「仕様上ではフラットトップ」と記載されていても有名メーカーのギターは実際にはトップ板が緩やかにラウンドしているタイプが多いです。理由は各メーカーによって違うと思いますが大まかに言うと強度の確保と音質の向上を図る為といったところではないでしょうか。
ちなみに自作するのは面倒くさいなと思う方は市販品もありますのでそちらを検討してみてはいかがでしょうか↓
スチュマック
LMI
それでは早速ラディアスディッシュの作り方です↓
まずはラディアスディッシュを作る為の冶具製作です。細かな作り方は省き、重要な部分のみ作り方や使い方を説明していきます。
まずこの冶具で重要なのは中央のMDF板(2枚)です。この板にはラウンド形状のガイドとなるカーブ加工がされています。この冶具を使用する時はカーブの部分にルーターを乗せて使用します。
※カーブ部分以外の外枠の寸法は作りたいラディアスディッシュのサイズに合わせて下さい。特に複雑な構造ではないので下記画像のみで作り方を判断して下さい。
カーブのついたMDF板の作り方↓
下記で製作しているのはトップ板用です。
ラウンド具合は40feet(半径約12m)で作っています。(Martinのトップ板のラウンドは40feetとか50feetとかいろいろな数値がネット上で言われていますが今回は40feetを選択)
まずMDF板(厚み12mm位~)を用意します。この板に実際にラウンドさせたい数値のカーブを書き込み削っていきます。
トップ用なので半径約12mの円周を書きます。
※MDF板の高さが高すぎるとラディアスディッシュ製作時にルーターの刃が届かない場合がありますので注意が必要です。
どうやって半径12mもの大きな円のカーブを書くのか?
ざっくり説明すると下記画像の用に支点を決め、ひもを利用してコンパスのようにカーブを書いていきます。最終地点にはペンを用意します。
画像では「糸」を使用していますが実際にはこれでまともなカーブは書けません。(書く時に糸が伸縮してカーブがゆがむ為)
そこで今回使用するのは伸縮の少ないPPバンドです。(梱包などで使用するやつ)
正直これでも中々綺麗に書けませんが何度も動かし方を練習すれば何とかなります。作業には広い場所の確保と、できれば「二人で協力」して行った方が上手くいくかもしれません。
僕は一人で行ったので支点となる部分を適当な板に釘付けしました。あと引っ張っても支点となる板が動かないようにブロックで固定しています。
最終地点(支点から約12m)からの画像↓
書く際はPPバンドにシャーペンの先端が入るぐらいの穴をあけ支点を中心に円を描くようにカーブを書きます。
※納得できるカーブを書くのには30分程かかりました。これよりももっと良い方法があると思いますのでチャレンジする人は各々アレンジして取り組んでみた方が良いかと。
下記がMDF板にカーブが書けたところ↓
こちらは書いたカーブに沿って加工した物↓
2個目は1個目を元にトリマーでトリミングするのですぐできます。これでカーブのついたMDF板部は完成なので最初の方で紹介した冶具にビスで固定します(センターも合わせる)。
クランプを使用しているのはビス止め時にズレがでない用にする為です。
次は土台となる平らな板とラディアスディッシュにする板を用意します。
こちらはラディアスディッシュに使用する板でMDF板2枚を貼り合わせた物を使用(厚みは約25mm)↓
コチラは土台となる平らな板で中心部には裏から釘を刺しています↓
中心の釘にはラディアスディッシュになるMDF板をはめます。
中心のアップ↓
ラディアスディッシュにする板の中心部には裏から穴をあけ釘がはまるようにします↓
穴のサイズは使用する釘と同じかもしくは少し小さい位が良いです。
差し込んだところ↓
この時に釘を刺したところを中心にスムーズに回転できるかを要確認。
※回転させる必要性は後の動画でチェック
セットした板の上にラディアスディッシュ製作用冶具を配置します↓
ラディアスディッシュとなる板の中心と冶具のセンターを合わせ、冶具は動かないように作業台に固定。
準備が整ったらルーターをMDF板のカーブ部に乗せ加工していきます。
中心から徐々に手前側へルーターを動かしながら掘っていき、この時にラディアスディッシュとなる板を回しながら作業をします。
加工時のイメージは下記動画を参考にして下さい。
動画ではすでに加工が完了しています。ルーターの動かし方や板の回転などに注目してご覧下さい。実加工時には左手の回転はもっと遅く回しながら行っています。また一度に掘る深さを多くしてしまうと刃の回転に板が振り回され大きなケガや事故に繋がるので要注意です↓
加工後は刃の跡や多少の段差などがあるので全体の形が崩れないように注意しながら紙やすりで整えていきます↓
紙やすりで整えた後↓
手で触ってみて滑らかになっていれば完成です。自作費用としては大体¥2,000前後といったところでしょう。
ばんば